Car body straightening work often comes down not only to basic skills in working with standard tools. Almost always, you will need to know the design features, the geometry of the body parts, and the observance of banal accuracy plays an important role. Even with a very rich experience and knowledge in this matter, you will need to use a special tool, which is a spotter.
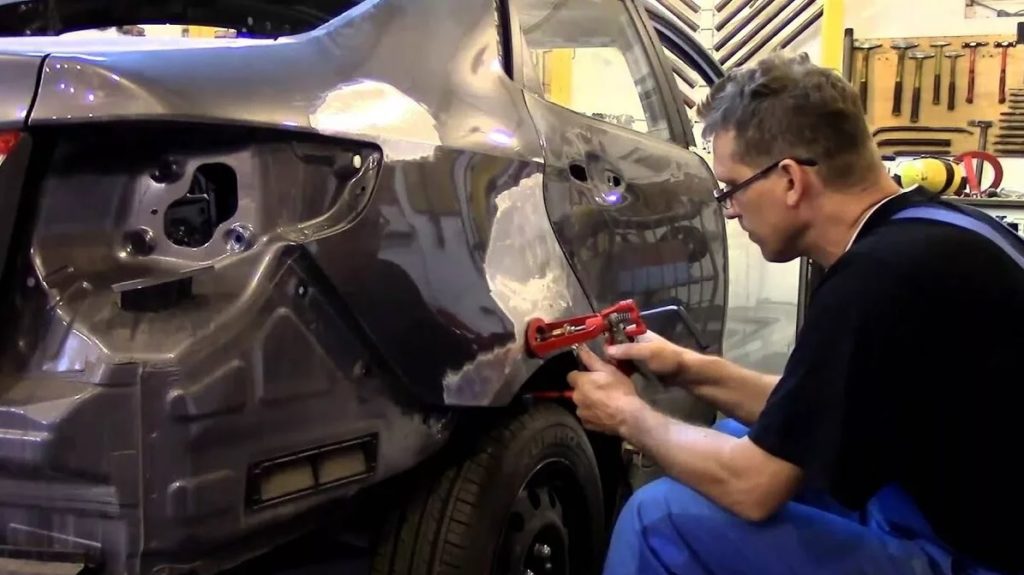
Spotter - general information
This word is used throughout the world for all types of resistance welding tools (from the English spot - "point"). In the former post-Soviet space, this is the name for one-sided welding machines used for repairing body surfaces of various types of vehicles, and which include a reverse hammer. The main purpose of using a spotter is to prevent the need to replace a damaged part, to carry out spot repairs instead, which saves on running costs.
Any professional straightener knows that spot welding is indispensable for complex body geometry. The surface on the machine with this tool is processed in any places, regardless of the difficulty of access. Working with the instrument is quite simple and does not require long training - that is why the devices are widely used.
The device, in fact, is universal - well suited for straightening body parts, such as: hood, sills, doors, fenders, etc. The main function of the device is to create a straightening force with fixation on the outside of the part.
Principle of operation and device
In a nutshell, a small section of a body element is heated with the help of a spotter, which must be eliminated from unintended deformation. At the same time, the car itself is caused a minimum of damage.
The simplest spotter tool consists of:
- Housings;
- Electric cable;
- Stadder nozzles;
- Ordinary electrode (it is possible to replace it with a pointed twist).
Any enclosure that is reasonably safe to work with can act as an enclosure. The spotter can be made independently, but such a device is unlikely to cope with long-term working conditions - only factory models are adapted to this.
The welding procedure includes the following steps:
- A fastener is attached (welded) to the damaged place;
- The machine's reverse hammer clings to the retainer;
- The stretching is performed using the muscular strength of the person, but sometimes additional tools are used.
The processing process itself does not require the application of special efforts and straightening is quite possible to carry out in a standard garage.
Types of spotters
In total, there are two main types of tools: transformer and inverter. Depending on the method and area of use, two more classes are distinguished: for body welding using the contact method and for straightening.
Straightening spotters are small devices designed for small work. They require the mandatory installation of a reverse hammer and additional attachments to complete the repair. In addition, the design may include special pliers. However, many of these devices have low power, are prone to rapid overheating, and therefore are not able to provide high-quality welding.
In addition, spot welding equipment can be classified according to the consumed supply voltage from the mains. Standard tools are rated at 220V, and the most powerful at 380V.
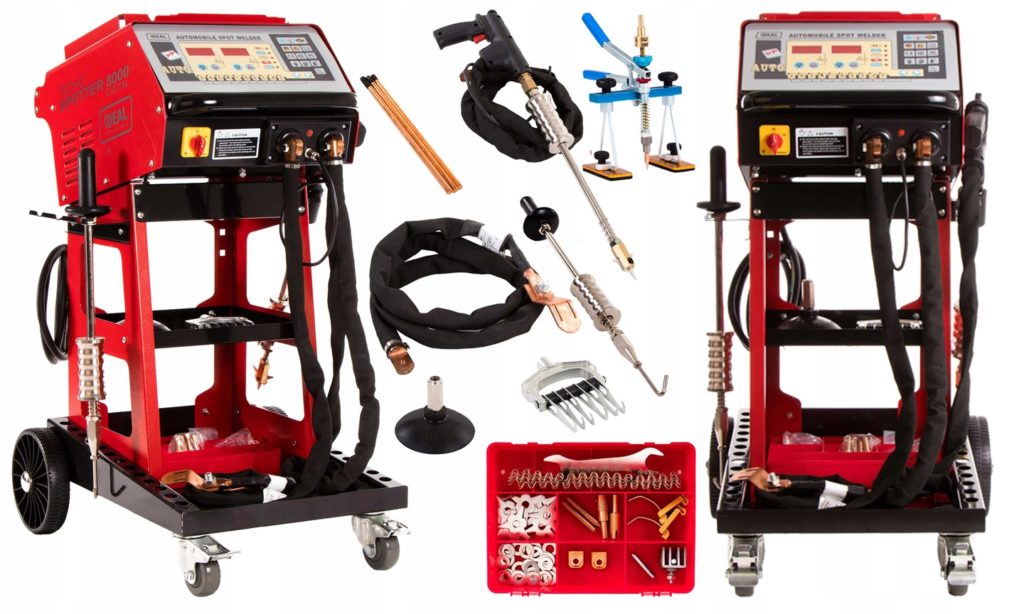
Detailed order of use
The work of smoothing the dent begins with the fact that the electrode is supplied with current from the welding machine. For straightening, a reverse hammer is used, which can be replaced with a pointed stop. The impact on the deformable surface must be carried out until it is completely leveled. Upon completion of all operations, the processing site must be cleaned, since there are electrode slags on it.
The algorithm for straightening work includes the following stages:
- Preparation of the treated surface (regardless of the material of the body - aluminum or iron), by removing any coatings from it, be it putty, paint layer, primer;
- Connection of the “negative” terminal from the device to the vehicle body for grounding purposes;
- Installation of fasteners, by welding various fasteners (loops, hooks and hooks) to the place of deformation, by means of spot welding;
- Preparation of equipment - coupling of the tool base and additional equipment is carried out (at this stage it is convenient to use a puller);
- Straightening the element, i.e. stretching it in order to restore its original appearance;
- Dismantling of fasteners - banal removal of fastening means (usually a "grinder" is used);
- The final stage is grinding, during which the surface is cleaned and preparatory work is carried out for subsequent painting.
To perform the above algorithm, minimal knowledge of working with a welding machine is sufficient. If the spotter is equipped with a set of nozzles, this will allow you to work with any fasteners.
Removing small dents
Despite the similarity of the algorithms of work, all works on a small scale have some differences, namely:
- For pulling, a single fastener is fixed;
- Cleaning is carried out only in the place of damage; it is better not to touch the surrounding area;
- Along the perimeter, the area to be treated is pasted over with a special (preferably painting) tape so as not to destroy the surrounding paint;
- Straightening is done effortlessly, again to avoid damage to the part as a whole.
It may be necessary to use additional attachments.
Elimination of deep damage
To eliminate such deformations, large-scale actions will be required, the distinctive features of which will be:
- Welding of more clamps in places of more severe damage;
- The stretching is done more slowly - little by little it is necessary to pull out "in a circle" each element. If one area is completely leveled, then when moving to another, the previous result may be destroyed;
- The reverse hammer is used in large sizes, however, heavy blows should still be avoided due to the risk of damage to the fasteners.
Functional focus of factory-made spotters
Their useful properties include:
- Perfectly interact in the process of straightening with repair washers;
- The metal electrode maintains the connection on a permanent basis for the subsequent rapid transition to operations;
- Works great with graphite electrodes;
- Comfort in use and ease of maintenance;
- They support switchable operating modes: long-term and short-term. In the first case, a metal electrode is used, or repair washers are generally used. In the second case, a carbon electrode is installed;
- They have their own cooling system, which will automatically turn off the device if it overheats.
Standard characteristics of serial spotters
These include the following variations:
- Power supply type - 220 V / 380 V network;
- AC frequency - 50-60 Hz;
- Maximum power - 10 kW;
- When welding, the maximum current strength reaches 1300 A;
- The voltage generated on the secondary winding is 8-9 V;
- The built-in timer can be set for a period of 0.1 to 1.2 seconds;
- They have the ability to switch welding modes from spot to permanent;
- The productivity of the device depends on the selected program - with precision, the device operates at maximum power, and with coal welding, the output power is minimal;
- By means of an iron electrode, the breaking force is more than 100 kg;
- When installing the repair washer, the pulling force is more than 100 kg.
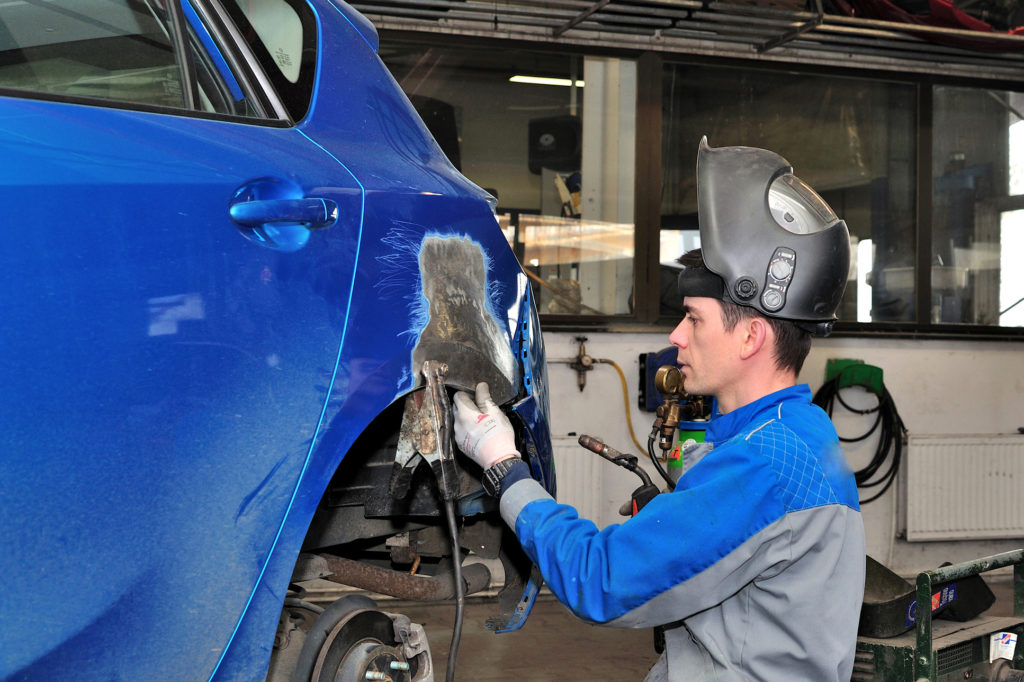
Completeness of spotter equipment
As a rule, devices made in China immediately come with the maximum number of accessories and attachments and are even equipped with a special trolley, so you don't have to buy anything.
At the same time, European models do not often boast a complete travel kit. However, due to the simplicity of the design of the tool itself, there are no problems in using "non-native" attachments when working.
Usually, in the design of equipment from Western manufacturers, a copper secondary winding of the transformer is necessarily used, which makes it possible to reduce power consumption at the same current, which significantly reduces the load on the network.
They are also equipped with special smart microprocessors, which will exclude possible erroneous metal burning. This function is especially relevant recently, when the world auto industry began to use metal sheets of very thin thickness (up to 0.6 mm.).
Parameters on which the spotter price depends
A huge role in the price of a spotter is played by parameters that indicate the current consumed by it, the general qualities of performance and functionality. The higher each of the listed parameters, the more and the price of the device. Thus, before buying, you should decide on the amount of work for which you need equipment. If one-time small work is expected, then you should not fork out for professional equipment. If it is supposed to constantly provide qualified services using this tool (for example, within the framework of the service station), then you should attend to the acquisition of powerful equipment.
Among the significant price factors, the following trend can be established:
- Transformer models are cheaper and more reliable, but tools with an inverter converter type are excellent in spot welding;
- Models with higher power are designed for spot welding and are used for stronger parts.Standard power will be quite enough for straightening single elements of the hull;
- The most expensive tools are with double-sided welding, in addition, it is performed using special pliers, which unfold on the back side and instantly create a hook.
Rating of the best spotting equipment for 2024
7th place: Pilot MT type MINI
One of the most budgetary, but at the same time reliable devices on the Russian market. At the end of 2019, it became the most demanded equipment among the devices of this type among Russians. Compatible with attachments from other manufacturers.
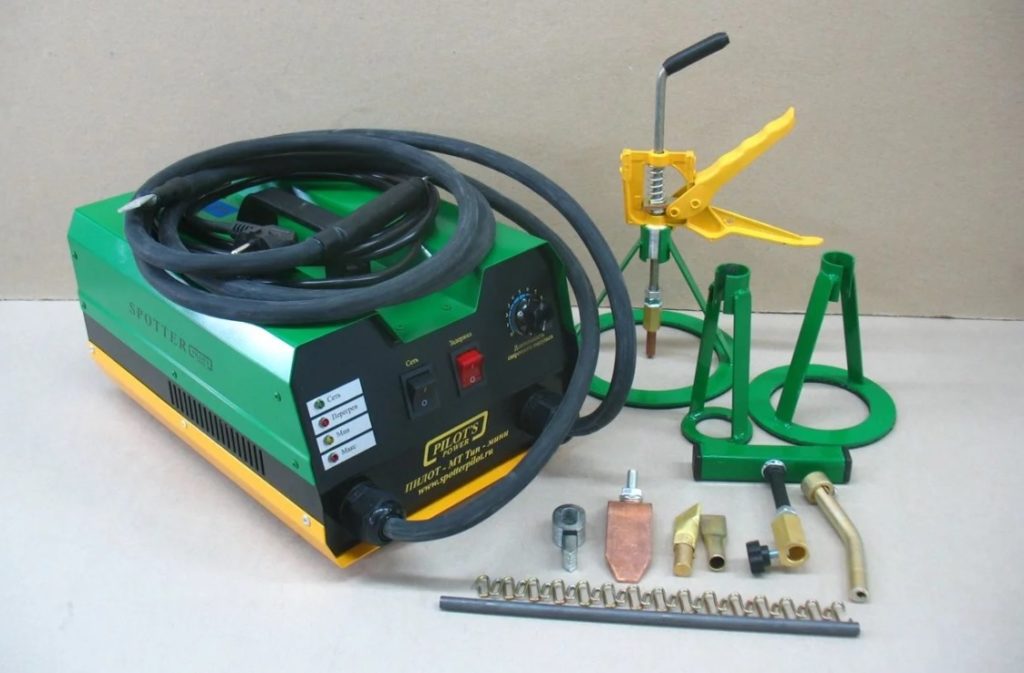
Specifications:
Name | Index |
Supply voltage, V | 220 |
Power consumption, W | 6 |
Current frequency, Hz | 50 |
Minimum welding current, A | 200 |
Maximum welding current, A | 1500 |
Maximum thickness of parts to be welded, mm | 2 |
Weight, kg | 14 |
Price, rub. | 14000 |
Pilot MT type MINI
Benefits
- Complete with its own set of nozzles;
- Works with both its own puller and third-party attachments;
- The kit includes 10 repair washers.
disadvantages
- It is forbidden to deposit metal with a copper electrode.
6th place: Elitech ATC 5
A highly specialized apparatus for car body repair. It is supposed to be used only in conjunction with a more powerful model, since its main function is to weld studs for subsequent straightening of parts using a reverse hammer.
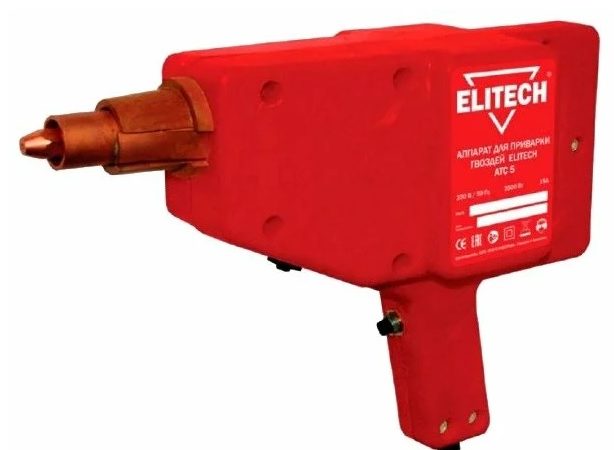
Specifications:
Name | Index |
Maximum current, A | 15 |
Power, W | 3500 |
frequency Hz | 50 |
Diameter of studs to be welded, mm | 2020-03-02 00:00:00 |
Weight, kg | 4 |
Class | "Semi-professional" |
Price, rub. | 8000 |
Elitech PBX 5
Benefits
- Compactness;
- Affordable price;
- Low power consumption.
disadvantages
- Narrow functionality (impossibility of welding even thin metal sheets together).
5th place: Fubag TS 3800
The tool is designed to remove dents from vehicle bodies. It gained well-deserved popularity due to its convenient pistol, the presence of a microprocessor discharge, and a simple control panel.
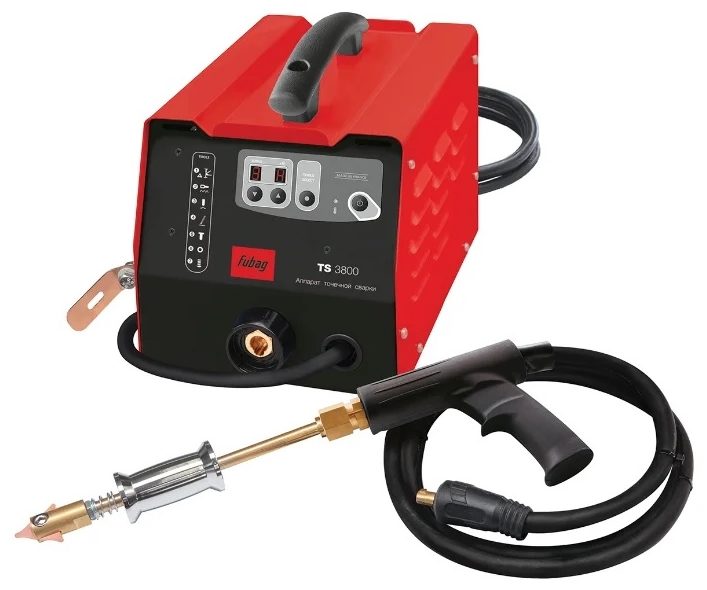
Specifications:
Name | Index |
Maximum welding current, A | 3800 |
frequency Hz | 50 |
Net weight, kg | 23 |
power, kWt | 7.4 |
Item height, mm | 235 |
Voltage, V | 220 |
Item width, mm | 360 |
Mains fuse, A | 16 |
Item length, mm | 225 |
Price, rub | 24600 |
Fubag TS 3800
Benefits
- 7 programmable modes for 11 power options;
- Overheating indicator;
- Low weight.
disadvantages
- A relatively short cable - only 4 meters.
4th place: Atis S52L
This multifunctional spotter is designed for tricky body straightening jobs. Equipped with overheating microprocessor and automatic input of welding mode. The main duty cycle of the device is designed for 10 minutes of operation at rated load, excluding overheating.
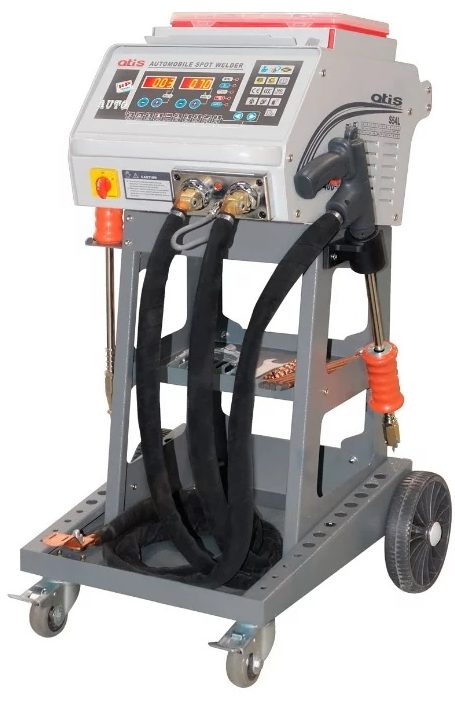
Specifications:
Name | Index |
Maximum current, A | 5200 |
Power, W | 20000 |
Thickness of sheets to be welded, mm | 2 |
Running time adjustment | machine |
Cooling | aerial |
Voltage, V | 220-380 |
Weight, kg | 78 |
Price, rub | 30000 |
Atis S52L
Benefits
- Increased compression force (180 kg);
- Automatic cooling mode;
- The presence of a convenient trolley for moving.
disadvantages
- Increased power consumption.
3rd place: Redhotdot Hammer T-26
Professional grade tool for fixing steel car panels. Allows for the smallest repairs that do not require disassembly of the machine. Has a comfortable pistol grip operating on an automatic charge and an intuitive control panel.
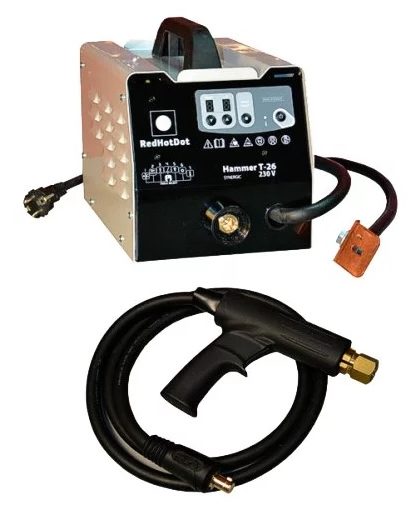
Specifications:
Name | Index |
Maximum current, A | 3800 |
Power, W | 5200 |
Welding adjustment | Machine |
frequency Hz | 50 |
Voltage, V | 220-230 |
Additionally | portable type |
Weight, kg | 24 |
Price, rub | 43000 |
Redhotdot Hammer T-26
Benefits
- Simplified system for setting the SINERGIC view;
- Connecting an additional tool using a Euro connector;
- Relatively light weight.
disadvantages
- Does not work well with third party attachments.
2nd place: Wiederkraft WDK-6000
An excellent tool for professional work in a car service. Fully copes with the performance of one-sided spot welding.It has increased power, the body is made in a dust and moisture protection version.
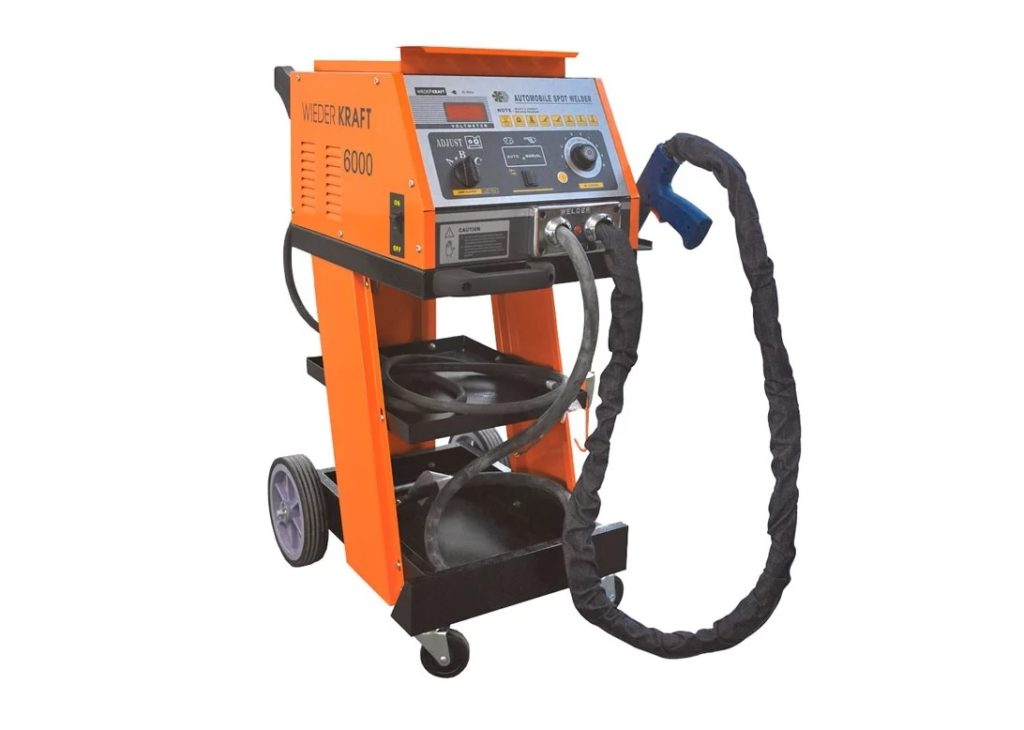
Specifications:
Name | Index |
Maximum current, A | 4400 |
Power, W | 11000 |
frequency Hz | 50-60 |
Weight, kg | 67 |
Additionally | manual adjustment of the welding time possible |
Price, rub | 46000 |
Wiederkraft WDK-6000
Benefits
- Professional device that does not impose special requirements on the knowledge of the operator;
- Provided with a comfortable trolley for movement;
- Intuitive customization.
disadvantages
- Extremely meager equipment.
1st place: Telwin Digital Car Spotter 5500
This professional unit has been specially designed for use in the auto repair industry. Focused on welding thin-walled metal (welding two sheets of 1.5 mm thickness is not a problem). Designed for correcting deformed surfaces and welding washers, screws and nails.
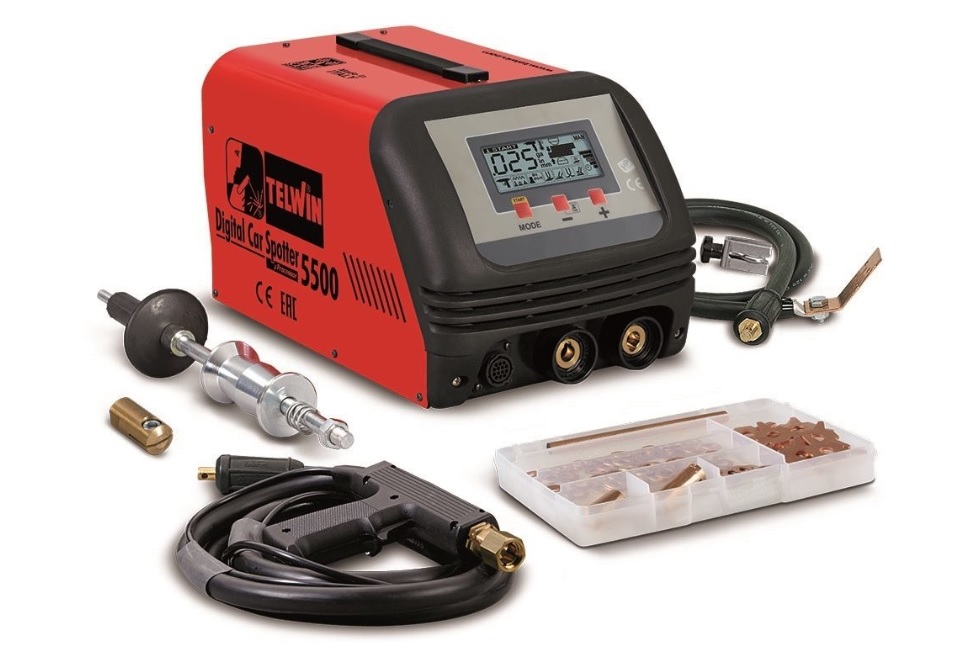
Specifications:
Name | Index |
Weight, kg | 30 |
Voltage, V | 380 |
Overall dimensions, mm | 390x260x225 |
power, kWt | 11 |
Welding current max, A | 3000 |
Power at 50% load, kW | 3.0 |
Thickness of materials to be welded (each) max, mm | 1.5+1.5 |
Price, rub. | 73000 |
Telwin Digital Car Spotter 550
Benefits
- Supplied complete with attachments designed specifically for body repair (Studder);
- Easy to set up;
- Has high power and performance.
disadvantages
- High price even for a professional tool.
Instead of an epilogue
In straightening works today it is simply impossible to do without spotters, because they significantly reduce the labor intensity of the process and improve the quality of work. You can buy them in any specialty store or order them on a trustworthy online trading platform (significant money savings are possible). The market for spotters and accessories for them is large enough, so choosing a model is not difficult. However, not all devices are complex technical goods, so simpler models will have a minimum warranty period.
A properly selected model, combined with a well-defined scope of work, will allow you to get the best result.